ABS from Butadiene, Acrylonitrile and Styrene (Hybrid Process)
Acrylonitrile Butadiene Styrene Production Costs Report | Issue C | Q4 2024
Report Details |
120 kta United States-based plant | Q4 2024 | 107 pages |
This report presents a cost analysis of a 120 kta (kilo metric ton per annum) United States-based plant. You can add a customized cost analysis, assuming another location (country), when ordering a premium edition of this report.
Report Abstract
In this report, the process examined for the Acrylonitrile Butadiene Styrene (ABS) production is a hybrid polymerization process in the United States. Initially, a solution of styrene and acrylonitrile is bulk prepolymerized with agitation. Polymerization is further conducted in suspension in water.
The report provides a comprehensive study of Acrylonitrile Butadiene Styrene production and related Acrylonitrile Butadiene Styrene production cost, covering three key aspects: a complete description of the Acrylonitrile Butadiene Styrene production process examined; an in-depth analysis of the related Acrylonitrile Butadiene Styrene plant capital cost (Capex); and an evaluation of the respective Acrylonitrile Butadiene Styrene plant operating costs (Opex).
The Acrylonitrile Butadiene Styrene production process description includes a block flow diagram (BFD), an overview of the industrial site installations, detailing both the process unit and the necessary infrastructure, process consumption figures and comprehensive process flow diagrams (PFD). The Acrylonitrile Butadiene Styrene plant capital cost analysis breaks down the Capex by plant cost (i.e., ISBL, OSBL and Contingency); owner's cost; working capital; and costs incurred during industrial plant commissioning and start-up. The Acrylonitrile Butadiene Styrene plant operating costs analysis covers operating expenses, including variable costs like raw materials and utilities, and fixed costs such as maintenance, labor, and depreciation.
Process Overview
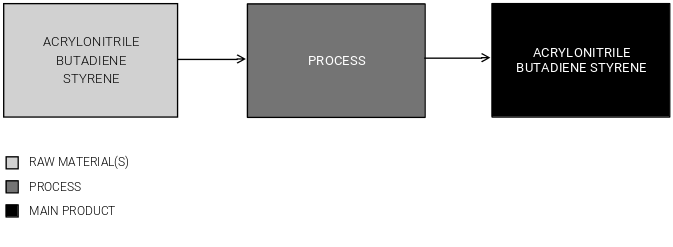
Product
Acrylonitrile Butadiene Styrene. Acrylonitrile Butadiene Styrene (a.k.a. ABS) is the largest selling engineering thermoplastic worldwide. ABS consists of a family of polybutadiene resin grafted with acrylonitrile and styrene. Property advantages from this polymer includes good processability, chemical resistance and thoughness. These properties can be optimized by adjusting the ratio of the three monomers which allows for incredible versatility to meet product requirements. While the polymer components coexist as two separate phases, ABS actually represents one of the industrially most important thermoplastic two-phase systems with an amorphous structure.
Raw Materials
Butadiene. Butadiene is a commodity mainly produced as a byproduct of ethylene crackers. More specifically, it is extracted from the C4 hydrocarbons stream in naphtha-based crackers. The largest single use of butadiene is in the production of SBR and styrene-butadiene latexes.
Styrene. Styrene is a largely available commodity generally produced from ethylbenzene by several means. One of the commercial routes for styrene production relies on the alkylation of benzene with ethylene for generating the ethylbenzene, which is then dehydrogenated to styrene in vapor phase with steam.
Acrylonitrile. Acrylonitrile is a molecule having a carbon-carbon double bond conjugated with a nitrile group. It is a very reactive compound, since it is polar (due to the presence of the nitrogen heteroatom) and unsaturated. Currently, acrylonitrile is mainly produced by the ammoxidation of propylene and by the ammoxidation of propane. Both processes generate acetonitrile and hydrogen cyanide as by-products. As a highly reactive chemical, acrylonitrile serves as an intermediate to produce a range of chemicals, including antioxidants, pharmaceuticals and especially polymers. Due to the possibility of spontaneous polymerization in the presence of strong alkali or when exposed to light, high-purity acrylonitrile product must be stored or transported with polymerization inhibitors. Storage tanks or containers may be constructed with carbon or stainless steel.
Up-to-date PDF Report
Professional report based on Q4 2024 economic data, ensuring timely evaluations.
Multiple Use Cases
Ideal for investment screening, feasibility studies, cost estimates, and research planning.
Proven Methodology
Developed using a consistent methodology honed over a decade, ensuring reliable cost analyses.
Compact
$1,199 USD
Production Process Information
Process Consumptions
Labor Requirements
Plant Capital Cost Summary
Operating Cost Summary
Production Costs Datasheet
Pages | Tables | Images
Read-only Online PDF Format
Updated with Q4 2024 Data
DETAILED
$1,999 USD
Production Process Information
Process Consumptions
Labor Requirements
Plant Capital Cost Summary
Operating Cost Summary
Production Costs Datasheet
Plant Capital Cost Details
Operating Cost Details
Pages | Tables | Images
Downloadable PDF Format
Updated with Q4 2024 Data
PREMIUM
MOST POPULAR
$3,399 USD
Production Process Information
Process Consumptions
Labor Requirements
Plant Capital Cost Summary
Operating Cost Summary
Production Costs Datasheet
Plant Capital Cost Details
Operating Cost Details
Plant Cost Breakdowns
Plant Capacity Assessment
Process Flow Diagrams
Costs in Different Countries Add-on
Pages | Tables | Images
Print-enabled PDF Format Add-on
Updated with Q4 2024 Data
Share with Co-workers
Technical Support via Email
Content Highlights
Plant Capital Cost Summary
Summary outlining the capital cost required for building the Acrylonitrile Butadiene Styrene production plant examined
Plant Capital Cost Details
Detailing of fixed capital (ISBL, OSBL & Owner’s Cost), working capital and additional capital requirements
Plant Cost Breakdowns
Breakdown of Acrylonitrile Butadiene Styrene process unit (ISBL) costs and infrastructure (OSBL) costs; plant cost breakdown per discipline
Operating Costs Summary
Summary presenting the operating variable costs and the total operating cost of the Acrylonitrile Butadiene Styrene production plant studied
Operating Cost Details
Detailing of utilities costs, operating fixed costs and depreciation
Plant Capacity Assessment
Comparative analysis of capital investment and operating costs for different Acrylonitrile Butadiene Styrene plant capacities
Production Process Information
Block Flow Diagram, descriptions of process unit (ISBL) and site infrastructure (OSBL)
Process Consumptions
Raw materials and utilities consumption figures, by-products credits, labor requirements
Process Diagrams
Process flow diagrams (PFD), equipment list and industrial site configuration
Other Acrylonitrile Butadiene Styrene Production Cost Reports
ABS from Butadiene, Acrylonitrile and Styrene (Emulsion Process)
This report presents the economics of Acrylonitrile Butadiene Styrene (ABS) polymer production in the United States using an emulsion process. In this process, butadiene is first polymerized in the presence of water, forming a latex. The polybutadiene latex is submitted to a grafting reaction with styrene and acrylonitrile monomers. The graft latex is mixed with a SAN Latex produced separately.
Details: 150 kta United States-based plant | Q4 2024 | 107 pages | Issue A From $1,199 USD
The cost analyses presented in this report target a 150 kta (kilo metric ton per annum per annum) United States-based plant. For those interested in cost analyses considering other plant capacities and/or locations, Intratec offers a customized analysis as an optional feature.
ABS from Polybutadiene, Acrylonitrile and Styrene (Mass Process)
This report assesses the economics of an industrial plant in the United States for the production of Acrylonitrile Butadiene Styrene (ABS) via a mass polymerization process. Initially, butadiene rubber is ground in a mill and dissolved in acrylonitrile and styrene. The mixture is submitted to a two-step copolymerization in the presence of a solvent.
Details: 120 kta United States-based plant | Q4 2024 | 107 pages | Issue B From $799 USD
The cost analyses presented in this report target a 120 kta (kilo metric ton per annum per annum) United States-based plant. For those interested in cost analyses considering other plant capacities and/or locations, Intratec offers a customized analysis as an optional feature.
Could Not Find the Report You Need?
Obtain a Bespoke Report
Get a report targeting the process in which you are interested
See Offer Details
Understand Bespoke Reports and how you can easily order them
Check Editions & Pricing
Complete a brief form and see a quotation for your Bespoke Report
Other Related Production Cost Reports
Styrene Production from Propylene & Ethylbenzene
This study presents the economics of Styrene production from chemical grade (CG) propylene and ethylbenzene in the United States. The process examined is a Propylene Oxide/Styrene Monomer (POSM) technology similar to the one owned by LyondellBasell. This process involves ethylbenzene oxidation, epoxidation, hydrogenation and dehydration steps.
Details: 850 kta United States-based plant | Q4 2024 | 107 pages | Issue B From $1,199 USD
The cost analyses presented in this report target a 850 kta (kilo metric ton per annum per annum) United States-based plant. For those interested in cost analyses considering other plant capacities and/or locations, Intratec offers a customized analysis as an optional feature.
Styrene Production from Ethane & Benzene (H2 as Co-Product)
This report presents the economics of Styrene production from ethane and benzene in the United States, with pure hydrogen as by-product. In this report, ethylbenzene (EB) is first generated from benzene and recycled ethylene. Then, fresh ethane and the EB are dehydrogenated to form ethylene and Styrene. The process analyzed is based on concepts proposed in patents issued to Dow and Snamprogetti.
Details: 750 kta United States-based plant | Q4 2024 | 107 pages | Issue C From $1,199 USD
The cost analyses presented in this report target a 750 kta (kilo metric ton per annum per annum) United States-based plant. For those interested in cost analyses considering other plant capacities and/or locations, Intratec offers a customized analysis as an optional feature.
Butadiene Production from n-Butane
This report presents the economics of 1,3-Butadiene (BD) production from n-butane. In the process, n-butane undergoes a dehydrogenation reaction process similar to Lummus Catadiene, generating a C4s stream which is purified to obtain 1,3-Butadiene. The economic analysis is based on a plant located in the United States.
Details: 100 kta United States-based plant | Q4 2024 | 107 pages | Issue A From $799 USD
The cost analyses presented in this report target a 100 kta (kilo metric ton per annum per annum) United States-based plant. For those interested in cost analyses considering other plant capacities and/or locations, Intratec offers a customized analysis as an optional feature.
Butadiene Production from Butenes
This study presents the economics of 1,3-Butadiene (BD) production from mixed butenes in a plant assumed to be erected in the United States. In this process, which is similar to TPC/UOP Oxo-D, butenes are catalytically dehydrogenated to produce the Butadiene product. Raffinate is obtained as by-product.
Details: 240 kta United States-based plant | Q4 2024 | 107 pages | Issue B From $799 USD
The cost analyses presented in this report target a 240 kta (kilo metric ton per annum per annum) United States-based plant. For those interested in cost analyses considering other plant capacities and/or locations, Intratec offers a customized analysis as an optional feature.
Acrylonitrile Production from Propylene (Fluidized Bed Ammoxidation)
This report presents the economics of Acrylonitrile production from chemical grade (CG) propylene in the United States. The process reviewed is a propylene ammoxidation technology using fluidized bed reactor, in which propylene reacts with ammonia, producing Acrylonitrile, and generating acetonitrile and hydrogen cyanide as by-products.
Details: 300 kta United States-based plant | Q4 2024 | 107 pages | Issue A From $799 USD
The cost analyses presented in this report target a 300 kta (kilo metric ton per annum per annum) United States-based plant. For those interested in cost analyses considering other plant capacities and/or locations, Intratec offers a customized analysis as an optional feature.
Acrylonitrile Production from Propane
This study presents the economics of Acrylonitrile production via propane ammoxidation. The process is similar to the one proposed by PTT Asahi Chemical (PTTAC), consisting in the reaction of propane with ammonia, producing Acrylonitrile. Acetonitrile and hydrogen cyanide are produced as by-products. The analysis assumes a plant located in the United States,
Details: 200 kta United States-based plant | Q4 2024 | 107 pages | Issue B From $799 USD
The cost analyses presented in this report target a 200 kta (kilo metric ton per annum per annum) United States-based plant. For those interested in cost analyses considering other plant capacities and/or locations, Intratec offers a customized analysis as an optional feature.
+800 Reports Developed, Targeting +250 Commodities
Best-in-Class Reports
Analysis of capital and operating costs of commodity production processes. Prices starting at $799 USD
Vast Report Library
858 independent and up-to-date reports examining embryonic and established production processes
Free Sample Reports
Quickly understand the structure and depth of content of our professional reports