Acetaldehyde Production from Ethylene (Single-Step Process)
Acetaldehyde Production Costs Report | Issue E | Q4 2024
Report Details |
70 kta United States-based plant | Q4 2024 | 107 pages |
This report presents a cost analysis of a 70 kta (kilo metric ton per annum) United States-based plant. You can add a customized cost analysis, assuming another location (country), when ordering a premium edition of this report.
Report Abstract
This report assesses the economics of Acetaldehyde production from ethylene in the United States using a typical single-step oxidation process. In this process, ethylene oxidation is carried out by using high purity oxygen.
The report provides a comprehensive study of Acetaldehyde production and related Acetaldehyde production cost, covering three key aspects: a complete description of the Acetaldehyde production process examined; an in-depth analysis of the related Acetaldehyde plant capital cost (Capex); and an evaluation of the respective Acetaldehyde plant operating costs (Opex).
The Acetaldehyde production process description includes a block flow diagram (BFD), an overview of the industrial site installations, detailing both the process unit and the necessary infrastructure, process consumption figures and comprehensive process flow diagrams (PFD). The Acetaldehyde plant capital cost analysis breaks down the Capex by plant cost (i.e., ISBL, OSBL and Contingency); owner's cost; working capital; and costs incurred during industrial plant commissioning and start-up. The Acetaldehyde plant operating costs analysis covers operating expenses, including variable costs like raw materials and utilities, and fixed costs such as maintenance, labor, and depreciation.
Process Schematic
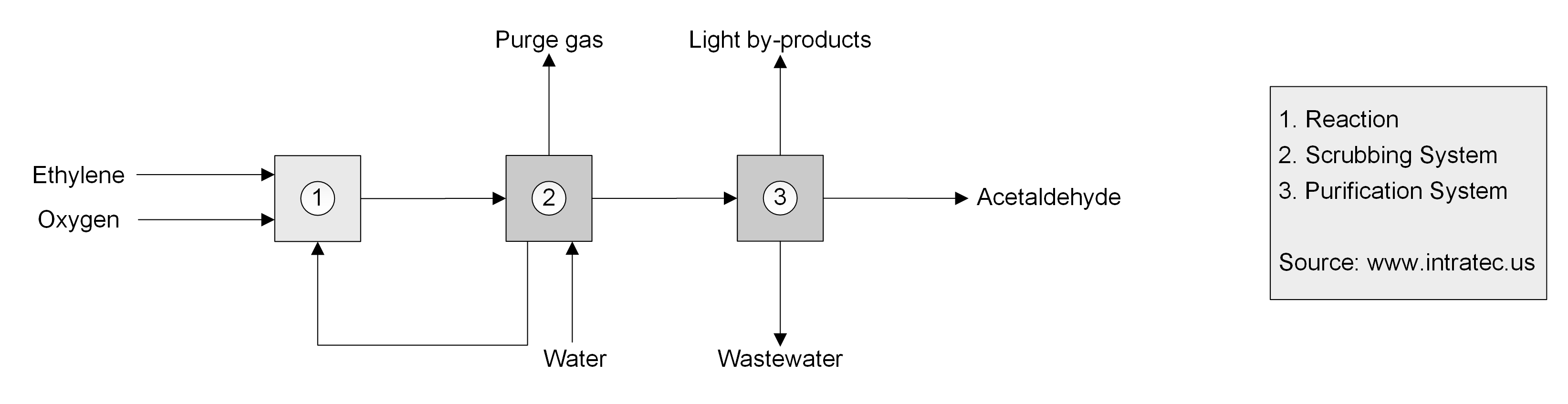
The process under analysis comprises two major sections: (1) Reaction; (2) Recovery and Purification.
Reaction. In the first section, ethylene and oxygen are fed independently to a vertical ceramic-lined reactor, and ethylene is oxidized to Acetaldehyde in the presence of an aqueous solution of PdCl2 and CuCl2, used as a catalyst. The reaction is conducted at 130 °C, and about 3-4 bar. A solution containing the catalyst and Acetaldehyde formed is partially vaporized in the reactor itself and then routed to a separator, in which the Acetaldehyde-water vapor mixture is separated overhead and directed to distillation steps downstream. The catalyst solution withdrawn from the separator bottom, is returned to the reactor, after part of the catalyst being regenerated.
Recovery and Purification. The Acetaldehyde-water vapor mixture from the separator is cooled and scrubbed with process water for the condensation and recovery of Acetaldehyde at the bottom. A large part of the gas leaving the Scrubbing System is recycled to the reactor, but a small part needs to be purged. The purged gas is led to a burner for energy generation. Crude Acetaldehyde recovered at the bottom has a low concentration and needs to be directed to the Purification System, where, after passing through two distillation columns, high-purity Acetaldehyde is obtained. In the first column, low-boiling substances are stripped off and burned for energy generation, while the Acetaldehyde stream obtained as column’s bottom is fed to the second column. In this column, water and higher-boiling by-products are removed. High-purity Acetaldehyde is drawn from the column overhead, condensed, and obtained as the main product.
Up-to-date PDF Report
Professional report based on Q4 2024 economic data, ensuring timely evaluations.
Multiple Use Cases
Ideal for investment screening, feasibility studies, cost estimates, and research planning.
Proven Methodology
Developed using a consistent methodology honed over a decade, ensuring reliable cost analyses.
Compact
$999 USD
Production Process Information
Process Consumptions
Labor Requirements
Plant Capital Cost Summary
Operating Cost Summary
Production Costs Datasheet
Pages | Tables | Images
Read-only Online PDF Format
Updated with Q4 2024 Data
DETAILED
$1,799 USD
Production Process Information
Process Consumptions
Labor Requirements
Plant Capital Cost Summary
Operating Cost Summary
Production Costs Datasheet
Plant Capital Cost Details
Operating Cost Details
Pages | Tables | Images
Downloadable PDF Format
Updated with Q4 2024 Data
PREMIUM
MOST POPULAR
$3,099 USD
Production Process Information
Process Consumptions
Labor Requirements
Plant Capital Cost Summary
Operating Cost Summary
Production Costs Datasheet
Plant Capital Cost Details
Operating Cost Details
Plant Cost Breakdowns
Plant Capacity Assessment
Process Flow Diagrams
Costs in Different Countries Add-on
Pages | Tables | Images
Print-enabled PDF Format Add-on
Updated with Q4 2024 Data
Share with Co-workers
Technical Support via Email
Content Highlights
Plant Capital Cost Summary
Summary outlining the capital cost required for building the Acetaldehyde production plant examined
Plant Capital Cost Details
Detailing of fixed capital (ISBL, OSBL & Owner’s Cost), working capital and additional capital requirements
Plant Cost Breakdowns
Breakdown of Acetaldehyde process unit (ISBL) costs and infrastructure (OSBL) costs; plant cost breakdown per discipline
Operating Costs Summary
Summary presenting the operating variable costs and the total operating cost of the Acetaldehyde production plant studied
Operating Cost Details
Detailing of utilities costs, operating fixed costs and depreciation
Plant Capacity Assessment
Comparative analysis of capital investment and operating costs for different Acetaldehyde plant capacities
Production Process Information
Block Flow Diagram, descriptions of process unit (ISBL) and site infrastructure (OSBL)
Process Consumptions
Raw materials and utilities consumption figures, by-products credits, labor requirements
Process Diagrams
Process flow diagrams (PFD), equipment list and industrial site configuration
Other Acetaldehyde Production Cost Reports
Acetaldehyde Production from Acetic Acid
This report presents the economics of Acetaldehyde production from acetic acid in the United States using a hydrogenation process over a palladium on iron oxide catalyst.
Details: 50 kta United States-based plant | Q4 2024 | 107 pages | Issue A From $999 USD
The cost analyses presented in this report target a 50 kta (kilo metric ton per annum per annum) United States-based plant. For those interested in cost analyses considering other plant capacities and/or locations, Intratec offers a customized analysis as an optional feature.
Acetaldehyde Production from Ethylene (Two-Step Process)
This report presents a techno-economic analysis of Acetaldehyde production from ethylene in the United States using a typical two-step oxidation process. In this process ethylene is oxidized by air to Acetaldehyde in tubular reactors, using a palladium/copper catalyst system.
Details: 70 kta United States-based plant | Q4 2024 | 107 pages | Issue B From $999 USD
The cost analyses presented in this report target a 70 kta (kilo metric ton per annum per annum) United States-based plant. For those interested in cost analyses considering other plant capacities and/or locations, Intratec offers a customized analysis as an optional feature.
Could Not Find the Report You Need?
Obtain a Bespoke Report
Get a report targeting the process in which you are interested
See Offer Details
Understand Bespoke Reports and how you can easily order them
Check Editions & Pricing
Complete a brief form and see a quotation for your Bespoke Report
Other Related Production Cost Reports
Ethyl Acetate Production from Acetaldehyde
This report examines the economics of Ethyl Acetate production from acetaldehyde in the United States via Tishchenko reaction, which refers to the dimerization of acetaldehyde in the presence of an alkoxide catalyst to form the ester.
Details: 100 kta United States-based plant | Q4 2024 | 107 pages | Issue D From $799 USD
The cost analyses presented in this report target a 100 kta (kilo metric ton per annum per annum) United States-based plant. For those interested in cost analyses considering other plant capacities and/or locations, Intratec offers a customized analysis as an optional feature.
Ethylene Production from Naphtha (Low Severity Steam Cracking)
This report presents the economics of a naphtha-based steam cracker, equipped with an electricity cogeneration unit. In this process, naphtha is thermally cracked at low severity conditions, maximizing propylene to Ethylene ratio. The analysis is based on a plant located in Germany.
Details: 800 kta Germany-based plant | Q4 2024 | 107 pages | Issue A From $799 USD
The cost analyses presented in this report target a 800 kta (kilo metric ton per annum per annum) Germany-based plant. For those interested in cost analyses considering other plant capacities and/or locations, Intratec offers a customized analysis as an optional feature.
Ethylene Production from Ethane
This report presents the economics of Polymer Grade (PG) Ethylene production from ethane in the United States. In the process under analysis, ethane is thermally cracked in pyrolysis furnaces through the use of steam, yielding Ethylene. A hydrogen-rich gas is generated as by-product.
Details: 1,200 kta United States-based plant | Q4 2024 | 107 pages | Issue B From $799 USD
The cost analyses presented in this report target a 1,200 kta (kilo metric ton per annum per annum) United States-based plant. For those interested in cost analyses considering other plant capacities and/or locations, Intratec offers a customized analysis as an optional feature.
+800 Reports Developed, Targeting +250 Commodities
Best-in-Class Reports
Analysis of capital and operating costs of commodity production processes. Prices starting at $799 USD
Vast Report Library
858 independent and up-to-date reports examining embryonic and established production processes
Free Sample Reports
Quickly understand the structure and depth of content of our professional reports