Propylene Production from Methanol (Methanol-to-Propylene Process)
Propylene Production Costs Report | Issue E | Q4 2024
Report Details |
560 kta United States-based plant | Q4 2024 | 107 pages |
This report presents a cost analysis of a 560 kta (kilo metric ton per annum) United States-based plant. You can add a customized cost analysis, assuming another location (country), when ordering a premium edition of this report.
Report Abstract
This report presents the economics of Polymer Grade (PG) Propylene production from methanol in the United States, using a methanol-to-propylene (MTP) process similar to Lurgi MTP. Initially, methanol is converted do dimethyl ether (DME), which is then converted to Propylene. Gasoline is generated as by-product.
The report provides a comprehensive study of Propylene production and related Propylene production cost, covering three key aspects: a complete description of the Propylene production process examined; an in-depth analysis of the related Propylene plant capital cost (Capex); and an evaluation of the respective Propylene plant operating costs (Opex).
The Propylene production process description includes a block flow diagram (BFD), an overview of the industrial site installations, detailing both the process unit and the necessary infrastructure, process consumption figures and comprehensive process flow diagrams (PFD). The Propylene plant capital cost analysis breaks down the Capex by plant cost (i.e., ISBL, OSBL and Contingency); owner's cost; working capital; and costs incurred during industrial plant commissioning and start-up. The Propylene plant operating costs analysis covers operating expenses, including variable costs like raw materials and utilities, and fixed costs such as maintenance, labor, and depreciation.
Process Schematic
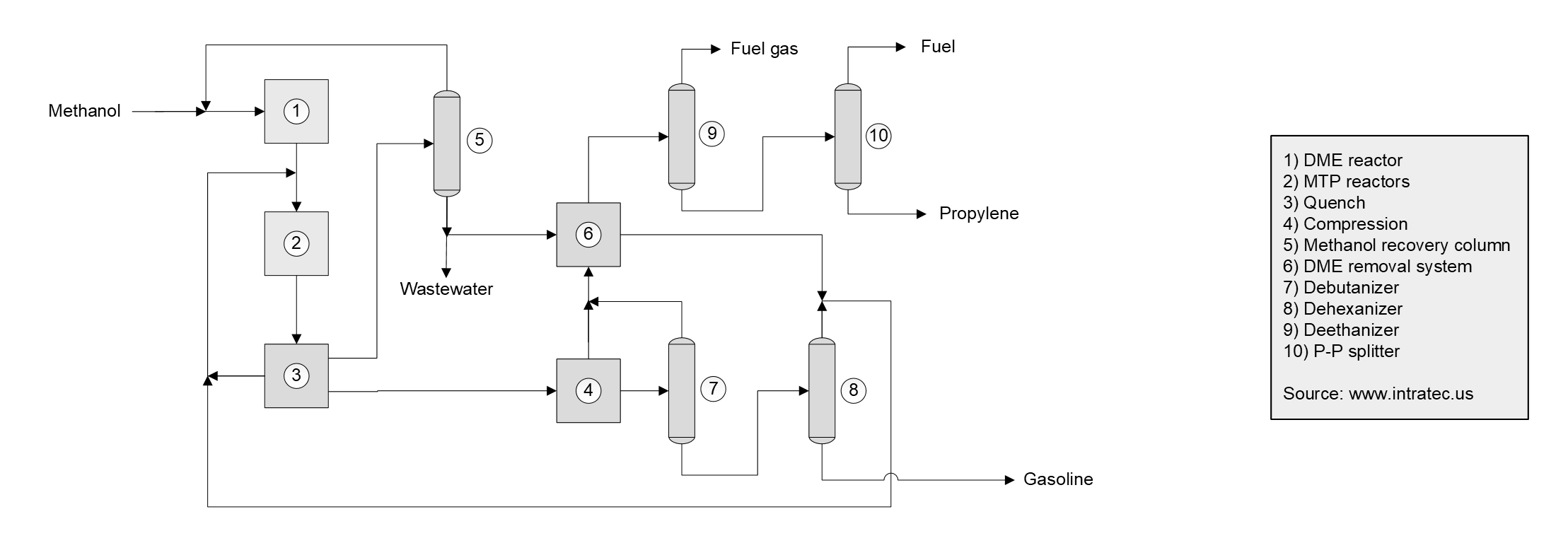
The process under analysis comprises three major sections: (1) Reaction and Regeneration; (2) Quench and Compression; and (3) Product Fractionation.
Reaction and Regeneration. The methanol feed is vaporized, mixed with recovered methanol and dimethyl ether (DME), superheated and sent to the DME reactor, where dehydration occurs. The product is mixed with recycled hydrocarbons and steam, before being fed into the MTP reactors. The reactors were designed with several stages for a better approach to isothermal conditions. Propylene synthesis is conducted in multiple reactors: while a set of ones conduct the reaction, the remaining are in regeneration or on stand-by mode. The recycle of olefins increases propylene yield and absorb the heat generated in the reaction. After leaving the reactors, the mixture is cooled and sent to the quench & compression steps.
Quench and Compression. The reactors outlet is quenched, where most of the water is removed. Part of this water is sent to the methanol recovery column, while the remaining is vaporized and used as dilution steam in MTP reactors. The vapor stream from quench is compressed, partially condensed, and separated into a liquid and a vapor streams.
Product Fractionation. The liquid stream from Quench & Compression is sent to the debutanizer, to separate C4- (hydrocarbons with 4 carbons or less) and DME from C5+ components. The C5+ stream from the column bottom is then separated (in the dehexanizer) into a C5/C6 stream to be recycled to the MTP reactors and into a heavier hydrocarbons stream (gasoline). The debutanizer overhead stream is mixed with the vapor stream from compression and sent to the DME removal system. The system overhead product, mainly propylene, is sent to the deethanizer, while the bottom is mostly recycled. The bottoms from the deethanizer is routed to the C3 splitter, to obtain PG propylene, while the overhead is recycled to the MTP reactors. The bottoms from the C3 splitter is purged as LPG.
Up-to-date PDF Report
Professional report based on Q4 2024 economic data, ensuring timely evaluations.
Multiple Use Cases
Ideal for investment screening, feasibility studies, cost estimates, and research planning.
Proven Methodology
Developed using a consistent methodology honed over a decade, ensuring reliable cost analyses.
Compact
$799 USD
Production Process Information
Process Consumptions
Labor Requirements
Plant Capital Cost Summary
Operating Cost Summary
Production Costs Datasheet
Pages | Tables | Images
Read-only Online PDF Format
Updated with Q4 2024 Data
DETAILED
$1,599 USD
Production Process Information
Process Consumptions
Labor Requirements
Plant Capital Cost Summary
Operating Cost Summary
Production Costs Datasheet
Plant Capital Cost Details
Operating Cost Details
Pages | Tables | Images
Downloadable PDF Format
Updated with Q4 2024 Data
PREMIUM
MOST POPULAR
$2,699 USD
Production Process Information
Process Consumptions
Labor Requirements
Plant Capital Cost Summary
Operating Cost Summary
Production Costs Datasheet
Plant Capital Cost Details
Operating Cost Details
Plant Cost Breakdowns
Plant Capacity Assessment
Process Flow Diagrams
Costs in Different Countries Add-on
Pages | Tables | Images
Print-enabled PDF Format Add-on
Updated with Q4 2024 Data
Share with Co-workers
Technical Support via Email
Content Highlights
Plant Capital Cost Summary
Summary outlining the capital cost required for building the Propylene production plant examined
Plant Capital Cost Details
Detailing of fixed capital (ISBL, OSBL & Owner’s Cost), working capital and additional capital requirements
Plant Cost Breakdowns
Breakdown of Propylene process unit (ISBL) costs and infrastructure (OSBL) costs; plant cost breakdown per discipline
Operating Costs Summary
Summary presenting the operating variable costs and the total operating cost of the Propylene production plant studied
Operating Cost Details
Detailing of utilities costs, operating fixed costs and depreciation
Plant Capacity Assessment
Comparative analysis of capital investment and operating costs for different Propylene plant capacities
Production Process Information
Block Flow Diagram, descriptions of process unit (ISBL) and site infrastructure (OSBL)
Process Consumptions
Raw materials and utilities consumption figures, by-products credits, labor requirements
Process Diagrams
Process flow diagrams (PFD), equipment list and industrial site configuration
Other Propylene Production Cost Reports
PG Propylene Production from RG Propylene
This report examines the costs related to Polymer Grade (PG) Propylene production from refinery grade (RG) propylene, via a typical purification process. Propane stream is generated as by-product. The economic analysis performed assumes a plant located in the United States.
Details: 400 kta United States-based plant | Q4 2024 | 107 pages | Issue J From $799 USD
The cost analyses presented in this report target a 400 kta (kilo metric ton per annum per annum) United States-based plant. For those interested in cost analyses considering other plant capacities and/or locations, Intratec offers a customized analysis as an optional feature.
Propylene Production from Butenes
This report analyses the economics of Polymer Grade (PG) Propylene production from raffinate-1 in the United States, using two typical integrated processes: isomerization and metathesis. In these processes, 1-butene present in raffinate-1 is isomerized into 2-butenes. The 2-butenes are submitted with ethylene to a metathesis reaction, producing propylene. A C5s stream is generated as by-product.
Details: 480 kta United States-based plant | Q4 2024 | 107 pages | Issue K From $1,199 USD
The cost analyses presented in this report target a 480 kta (kilo metric ton per annum per annum) United States-based plant. For those interested in cost analyses considering other plant capacities and/or locations, Intratec offers a customized analysis as an optional feature.
Could Not Find the Report You Need?
Obtain a Bespoke Report
Get a report targeting the process in which you are interested
See Offer Details
Understand Bespoke Reports and how you can easily order them
Check Editions & Pricing
Complete a brief form and see a quotation for your Bespoke Report
Other Related Production Cost Reports
Methanol Production from Natural Gas (Steam Reforming)
This study presents the economics of large-scale Methanol production from natural gas in the United States. In the process examined, natural gas is first converted into synthesis gas (syngas) by means of conventional steam reforming and then the syngas is converted into Methanol.
Details: 1,000 kta United States-based plant | Q4 2024 | 107 pages | Issue A From $799 USD
The cost analyses presented in this report target a 1,000 kta (kilo metric ton per annum per annum) United States-based plant. For those interested in cost analyses considering other plant capacities and/or locations, Intratec offers a customized analysis as an optional feature.
Methanol Production from Natural Gas (Combined Reforming)
This study presents the economics of large-scale Methanol production from natural gas in the United States. In this process, natural gas is first converted into synthesis gas (syngas) by means of conventional steam reforming and secondary autothermal reforming. Then, the syngas is converted into Methanol.
Details: 1,700 kta United States-based plant | Q4 2024 | 107 pages | Issue B From $799 USD
The cost analyses presented in this report target a 1,700 kta (kilo metric ton per annum per annum) United States-based plant. For those interested in cost analyses considering other plant capacities and/or locations, Intratec offers a customized analysis as an optional feature.
PP Homopolymer from Propylene (Spheripol)
This report presents the economics of Polypropylene (PP) Homopolymer production from polymer grade (PG) propylene. The process under analysis uses a bulk phase polymerization process similar to LyondellBasell Spheripol and Mitsui Hypol II. The economic analysis performed assumes a plant located in the United States.
Details: 350 kta United States-based plant | Q4 2024 | 107 pages | Issue A From $799 USD
The cost analyses presented in this report target a 350 kta (kilo metric ton per annum per annum) United States-based plant. For those interested in cost analyses considering other plant capacities and/or locations, Intratec offers a customized analysis as an optional feature.
PP Homopolymer from Propylene (Spherizone)
This report examines the costs related to Polypropylene (PP) Homopolymer production from polymer grade (PG) propylene, using a gas phase polymerization process similar to LyondellBasell Spherizone. The reaction occurs in a multi-zone circulating reactor (MZCR). The economic analysis performed assumes a plant located in the United States.
Details: 350 kta United States-based plant | Q4 2024 | 107 pages | Issue C From $799 USD
The cost analyses presented in this report target a 350 kta (kilo metric ton per annum per annum) United States-based plant. For those interested in cost analyses considering other plant capacities and/or locations, Intratec offers a customized analysis as an optional feature.
+800 Reports Developed, Targeting +250 Commodities
Best-in-Class Reports
Analysis of capital and operating costs of commodity production processes. Prices starting at $799 USD
Vast Report Library
858 independent and up-to-date reports examining embryonic and established production processes
Free Sample Reports
Quickly understand the structure and depth of content of our professional reports